

Higher flow will pull in cooler water from the radiator more easily and faster into the hot coolant circulating within the engine blocks galeries, of course flow limited and controlled by the thermostat.ģ. Higher flow reduces hotspots, and temperature differentuals in the engine.Ģ. And as we all probably know, the RB30/VL pumps resemble a vl pump but without the disc supporting the blades.įlow data is important for a number of reasons.ġ. Im interested in hearing everyones thoughts, and if you have actual flow data by all means post it up! Granted a big part of the reasoning behind this is to turn the fan faster so the engine will get propper cooling when spinning all 4 weeks and bogged to the axels in mud. They run a smaller pully size again than the VL's but on the same pump. There is also the Patrol RB30's to consider. But on a smaller displacement engine that typically revs around ~3000+ in typical in traffic driving, the N1 is adequite. Which leads me to think the N1 pump is not at all suitable for a big torque stroker engine, as sufficent coolant flow may not be possible when the engine is operating around 1500-2200 rpm. It also stands to reason the N1 pumps whilst being able to maintain sufficent coolant flow at 9000 rpm on an RB26 configured engine, may also just barely deliver enough coolant flow at low speeds. Resulting in a more even engine temperature (less variation) from the block to the head. So the thinking is, that a stock pump/pully configuration will actually be more "streetable" for most applications, as it will provide more flow at lower RPM. So turning the pump slower will mean less cavitation risk at higher RPM, whilst possibly achiving a lower flow rate. Which stands to reason as the skyline engines are designed to rev more. I've always seen people in high hp/high rpm applications (Nissan RB26 N1 water pump for example) try to decrease cavitation for better cooling going around a track at the expense of low rpm flow due to the design of the blades.Īlso of interest is that the RB20/25/26 pumps are turned at a lower average speed due to the pulley size being larger, compared with the VL/RB30 pumps. Others comments posted claim the N1 pump has higher flow, but do not offer an explanation or any real data other than the belief that N1 = Race car stuff = MORE POWER = MORE COOLING. about the only moderately *useful* bit of information. Search results have come up with this quote below. N1 is 6 blade with an anti-cavitation disc.
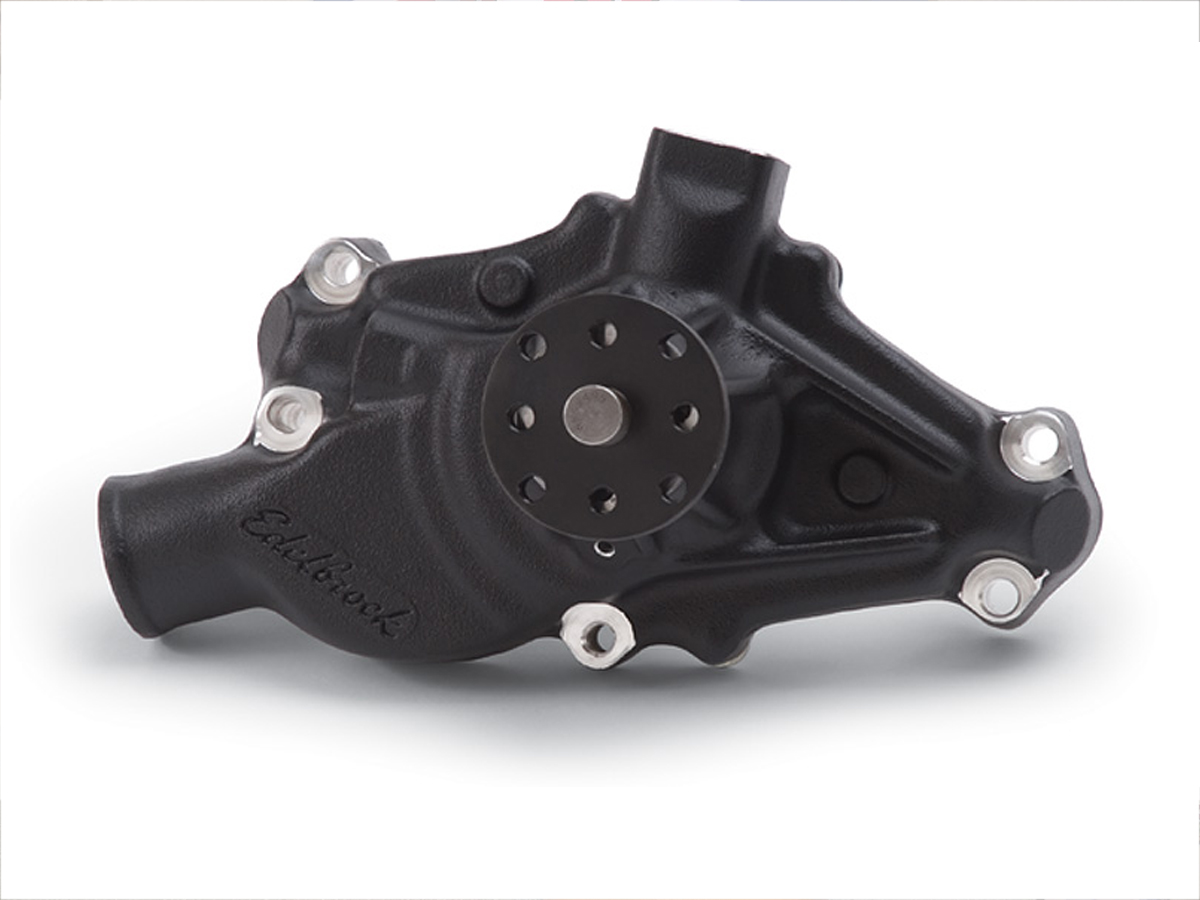
The VL/RB30 pumps are 6 blade and all RB20/25/26 pumps are 8 blade. Seems that oil pump data is everyhere to be found, but there is little said about the flow capabilities of the various coolant pumps. Im trying to track down some REAL flow data for the RB water pumps. I am also thinking of putting 3 temp sensors in the spacer plate of my next engine to get a picture of what is happening cooling wise around each of the cylinders. Where this thought came from is that I have been experimenting with different pully sizes on my open deck engine (which has the N1 water pump).
